SUPPORT EQUIPMENT REPAIRS
O ur leadership in test cell repair was already well established prior to the granting of the Indefinite Delivery, Indefinite Quantity (IDIQ) Repairs and Support contracts thanks in part to Atec’s 24/7 Toll-Free Hotline, Electronic problem reporting, Remote troubleshooting assistance, 130+ engineers expert in Test Cell and Tarmac engine test, and the most experienced Field Services teams in the business.
REPAIR, SUSTAINMENT & MODIFICATION OF ENGINE TEST EQUIPMENT & TEST CELLS
Speedy maintenance matched with long term Sustainment is emphasized to improve readiness. Configuration control and compatibility fosters field effectiveness. Obsolescence is addressed with compatible technology refreshment during timely repairs. We are committed to best value continuous incremental improvement for our repairs and sustainment customers.
Atec has doubled the size of our field service group to ensure timely performance. We now have field offices in London, Dubai, Singapore and Istanbul, with more coming. Additionally, we have enlarged our inventories of long lead items to accommodate client needs. We emphasize quick repairs that put broken equipment back in service first, followed by other needed maintenance and sustainment program work.
Vital Link, Inc. is a new subsidiary. Their field teams dealing with test cells & hush houses are widely praised by the military and commercial customers worldwide. Vital Link Europe offers full services from our London and Middle East locations, involving turnkey green field test cell construction through Mods, MSAs and site surveys.
Atec, Inc. has a strong reputation in the Turbine Engine Test Cell Industry that is built upon a very high degree of service and quality over a 65 year history. We can handle your Test Cell, Noise Suppressor and associated equipment repairs, maintenance and upgrade modifications.
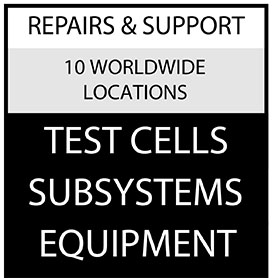
Need On-Site Assistance?
On-site repairs can vary depending on the state of the equipment and complexity of the repair. These are coordinated with our Field Services, Manufacturing, and Engineering departments.
Contact a Contracts Administrator for the initialization of a field repair, or get urgent assistance via our 24/7 Hotline at 1-877-514-2218.

Atec, Inc., as a responsible OEM, strives to offer repair services for all currently fielded equipment including legacy and obsolete gear. Now joined with Celtech and Vital Link, we support over 38,000 NSNs, 60+ years of legacy gear and the most modern systems at 10 locations internationally. Energy customers also benefit from the repair experience of Hager Machine & Tool, Celtech, Vital Link and Atec in oil patch equipment. Factory repairs can be conducted at Atec’s factory in SW Houston (Stafford) TX, Hager’s shop in North Houston TX, Vital Link’s campus in Sealy TX, Celtech’s plant in Carlsbad NM and VLE’s shop near London, UK. Our field service representatives are equipped and ready to meet your servicing needs worldwide, and have the full consultation of our 100+ engineers at our manufacture plants. Initial phone consultation with our technicians can provide telephone troubleshooting, as well as guidance on any evaluation of the equipment needing repairs. Where pre-repair evaluations are conducted, repairs are not undertaken until evaluations are transmitted to our clients, repair options priced and approved client instructions are received.
Equipment that is repaired at Atec, Celtech, Vital Link and Hager facilities follows the following ISO9001 process:
- Purchase order is received from the Customer initiating equipment evaluation.
- Equipment is received and inspected for shipping damage. A receiving inspection report is generated and the equipment is tagged as Customer Owned Material.
- The equipment is evaluated against the standard Acceptance Test Procedures used on new equipment. All deviations are noted and an Evaluation Report is generated along with the recommended repair process and materials.
- The repair is quoted to the customer to allow for a cost analysis to be performed.
- If the repair is approved, the equipment is moved to a Production Work Order and the repair process flows through the same process as current production work.
- Once the repair is complete, the item is tested per the Acceptance Test Procedure and inspected by the Quality Assurance Department. Final Repair Reports are generated and the repaired item is shipped back to the customer.