CONSTRUCTION
Construction has been in Atec’s blood since before its founding in 1953. Our founders were principal participants in famous construction projects like the Astrodome, the Vehicle Assembly Building and Crawler at Cape Canaveral, the Johnson Space Center, AEC Nuclear Test Reactor at Idaho Falls, a Coca Cola bottling plant, and dozens of Petrochemical plants. In Atec’s early days, we built the original Tinker AFB automated test cells, upgraded the Corpus Christi Army Depot cells, accomplished the first overhead test A/F37T-10 at McClellan AFB, and put in service state of the art fighter engine test rigs from Edwards AFB to NAS Pax River to Fort Worth JRB.
Vital Link, Inc. has joined our corporate team in 2017, with over 30 years of military construction history. VLI’s experience in hush houses and noise suppressors is world leading, with locations in Texas, England and UAE. Their field teams and large scale steel fabrication are highly respected. Beyond project work around the globe, Vital Link represents the USAF for noise suppressor repairs worldwide.
Atec can undertake any AeroEngine Test Cell project. Our linkages to SMEs, niche subcontractors and the world’s largest engineering & construction firms are very strong. Atec has active relationships with all major aeroengine OEMs. Our company can design, build, or modify your test cell, and assist you in getting the approved OEM specific input and equipment required. We can coordinate all parties to assure that cost savings, quality, safety, environment, schedule and maintenance goals are achieved.
More recently, our construction efforts have included paradigm shifts in facility technology. Atec innovated successful design modifications for two moved A/F32T-9 hush houses for testing the world’s best JSF/135 engines. Our Phoenix™ modular and single point lift facilities have been innovated by Atec for engine test cells and control rooms. Atec’s packaged utility systems for air, fuel, oil, and electric offer operating and green advantages. Our SuperLean TiltWall ™ concrete facilities made with proprietary formulations and connections offer non-corrosive strength, flexible usage, and high noise attenuation at low cost. Our renowned closed-loop 24/7 hotline provides our customers support with their urgent field problems, even after the sale.
The tilt-wall construction of the 10-Meter Turbofan Engine Test Cell for Kalitta Air Cargo is just one example of the innovation that Atec offers its clients. The standard U-shaped configuration houses a 10-meter by 10-meter cross section that allows the suspension of large bypass turbofan engines for testing. Kalitta provided many pieces of hardware for reutilization in the project, which involved detailed inspection, evaluation, cataloging, servicing, refurbishing, and implementation of each piece by Atec’s engineers and technicians to determine what could be used in the facility. Reusing equipment, whenever possible, significantly reduced the overall cost of the project. Atec’s renowned checklists are utilized to make sure site surveys, design meetings, installations, startups, spares and maintenance schedules are comprehensive.
Atec conducted a feasibility study, provided a conceptual design, and began construction using pre-engineered, pre-stressed, tilt-wall concrete panels atop a poured concrete foundation. The on-site construction time of the facility was reduced by an estimated 50% using the tilt-wall (pre-cast) construction method, as compared to traditional poured concrete methods.
Project and construction services have moved to an emphasis on joint planning, adherence to best practices and regulations, optimal results, and lasting customer satisfaction versus the older lowest bid method, where the interests of project parties can be inherently different. Collaborative efforts between User/Customer and Builder are now prevalent. Customer preferred application of health and safety requirements, environmental programming, community relations, labor and employment policies, insurance and legal needs, local supplier/subcontractor participation and financing preferences can all be carefully addressed as a team with Collaborative Contracting. Teamed scoping and estimating now begin most projects. Project management is continuous from scoping through completion and maintenance.
Registered General Contractor
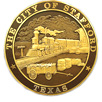
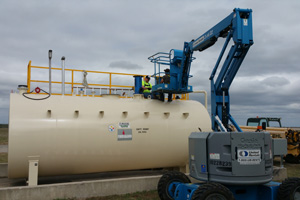
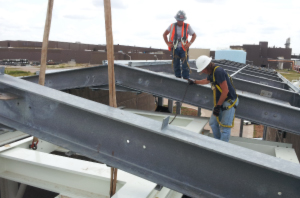
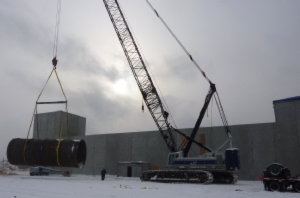
Pre-Project Services
- Project Management
- Site Surveys
- Estimating Workups
- Consultant Selection
- HSE Planning
- Contracts Definition
- Documentation Reviews
- Feasibility Studies
- Project Communications Setup
- Milestones Identification: as major considerations come into focus, the Customer and Atec collaborate to maximize project success
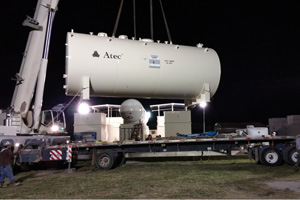
Project Services, Safety & Environmental Processes
- Affirmative Procurement & Recycling
- Local Supply, Subcontracting & Servicing
- Construction Management
- Detailed Definition
- Phasing and Scheduling
- Reports, Permits & Fees
- Procurement & Inspections
- Documentation & Submittals
- Safety & Environmental
- Contracts Administration
- Project Accounting
- Design Engineering
- Heat, Stress, Flow, Noise, Harmonics, Logistics and Capacity Studies
- Virtual Renderings & 3D Modeling
- Routing & Placement Conflicts Analysis
- LEEDS and Operating Safety Impacts
- Closeout/Warranty
- Maintenance Service Agreements/General Service Agreements
PROJECTS
Atec is experienced at design-build, project/construction management, Subject Matter Experts (SME) and architectural coordination, collaborative contracting, scheduling, site development, large fabrication, procurement, rigging, specialty subcontracting, inspection, integration, and commissioning to other project success.
Atec has the team of people needed to handle demanding construction and field service projects, as well as the manufacture of best in class operating equipment. Three dozen employees form the nucleus of our active construction and field team, which also includes important consultants/SMEs, general contractors, specialty subcontractors and craftsmen. Our team handles work worldwide, and we are well-experienced in foreign project accomplishment. From our storied roots, Atec has unexcelled access to major construction teammates. For aero engine test applications, here is a sampling of some of Atec’s projects over the years:
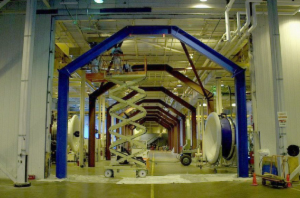
PROJECT SAMPLING
Kalitta Air Freight – Atec collaborated with Kalitta in a design-build project for a 10 meter test cell (Depot) in Oscoda, Michigan. Atec’s Super Lean 10M Tilt Wall cell offers masonry noise reduction, permanence, usage flexibility, and major cost savings to Kalitta. Atec’s ADAQ™ control system and software is now handling test runs for 5 different commercial engines.
Tinker JSF A/F32T-9s – Atec performed a design-build project for two modified T9 Hush House test cells (Depot) for the USAF in Oklahoma City (OKALC). Atec coordinated disassembly and shipment from foreign and domestic locations, and reviewed site work and foundations by Downey Construction at Tinker AFB. Facility and utilities work were accomplished directly by Atec as prime contractor. Other subcontractors were coordinated. Numerous facility and systems innovations were offered by Atec to accommodate the incredible F135 engines.
Delta Airlines/Pratt & Whitney – Atec was contracted by Pratt to turnaround a major jet engine test cell complex (Depot) upgrade project originally undertaken by Cenco. Atec oversaw and managed all technical aspects of the job in close coordination with Pratt, the site—work and structural (general) contractor, the doors manufacturer, the crane/rigging sub contractors, the mechanical and electrical sub contractors, etc. Test Cells 3 & 4 were enlarged and equipped to run V2500, CF6, CF34, JT9, PW2000, PW4000, CFM56-3, CFM56-7. The APU test rigs were modified, new doors, strong backs, and exhausts were installed, and a facilities control PLC system implemented. DAS and utility systems were also upgraded.
Rolls Royce – Atec designed, constructed, and installed two of our Phoenix™ modular test cells for Roll’s A250 & RR300 turboshaft post production testing at their Indianapolis factory (Depot). These cells were built and fully tested at Atec’s plant, transported by trucks to Indianapolis. The foundations was then poured, and cells were installed and commissioned by Atec. These cells have been in service since mid-2008, testing engines daily, with minimal service calls in over 6 years to date. These cells utilize Atec’s state of the art electric dynamometer regeneration system, helping power Roll’s Indy campus during engine testing which often occurs during peak electric load periods.
Burns & McDonnell –Atec was called in to verify correct quality and specification compliance on jet engine test cell systems and equipment under original contract from Burns & McDonnell to another test cell contractor. The equipment was later accepted and installed for the US Navy at Beaufort, SC following Atec’s efforts. Atec later built for Burns utilities systems—air, fuel, oil, electrical and tanks for Meridian and Kingsville NAS T-10 Hush Houses. Since then, Atec has been involved in numerous projects for the Navy at Jacksonville, Cherry Point, New River and China Lake.
USAF– Atec was selected to complete a A/F32T-4 Hush House prototype modernization contract for the USAF/AETC. Atec is responsible for completing the design and providing most internal systems—mechanical and electronic, updated documentation and onsite installation/construction at Laughlin AFB in Del Rio, TX. Atec engineers have updated drawings, provided concrete analysis, supervised concrete work, examined conduit, and provided onsite field welding. Project completion is scheduled for Q2 2016.